Benefits of Using the Linear Slide Assembly Systems
- Kim Jefersson
- Aug 26, 2020
- 3 min read
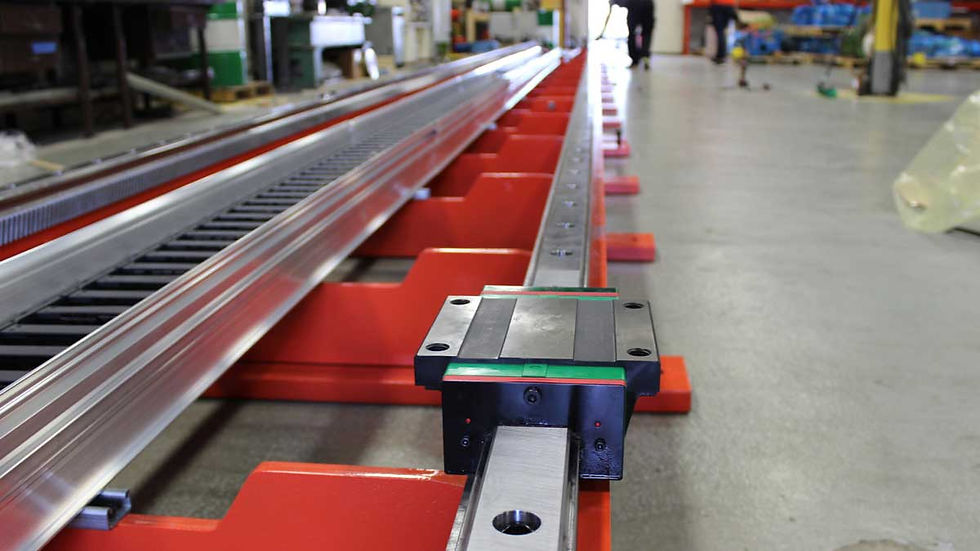
Linear slide assembly reduce maintenance and friction costs while maximizing lifecycle and accuracy. Available in a variety of styles to suit most industry applications, these sliding motion assemblies are used in machine tool, semiconductor, biomedical, life sciences, solar and aerospace industries. They are also used extensively in automotive industries, aerospace and in industrial and defense applications.
Slides have the ability to be either horizontal or vertical. This enables them to provide maximum versatility when it comes to use. For example, in semiconductor applications, a horizontal slide is ideal. For use in automotive applications, a vertical slide is better suited.
The key benefits of linear motion assembly are its long life, improved reliability, reduced manufacturing costs, ease of installation, and the ability to maintain high precision over long operational periods. It also minimizes wear and tear on parts, and is available with many different types of mechanisms. The slide mechanism is the main component and usually consists of three main elements - the slide, the moving rollers and bearings, and the bearing housing.
The main components of slide systems include the slide, the moving rollers and bearings, and the bearing housing. The moving rollers are the moving components in the slide system that are responsible for providing linear movement. These rollers are typically fixed or are movable by a torsion bar. Fixed roller mechanisms can only be mounted in one position, while adjustable mechanisms can be moved from one position to another. The roller housing, provides an additional buffer between the roller and the bearing housing, which provide an anti-slip surface.
In order to provide improved performance, linear motion assembly requires a complete assembly of moving rollers, bearing housing, bearing rollers and bearings, and the moving roller assembly. Each element of the sliding assembly should be designed for maximum performance. If one or more elements fail to perform, the entire assembly will not function properly, potentially resulting in increased wear and tear on the bearing housing.
Due to the mechanical parts' sensitivity, they can be easily broken or damaged if mishandled. This causes unnecessary downtime and can cost time and money. Therefore, quality control of all components is essential.
Because roller assemblies are made of two-dimensional solid materials, they require low friction, making them a good choice for both moving and stationary applications. Although they are more expensive than similar sliding motion assemblies, they offer long-term cost savings and lifetime performance advantages.
In addition to roller systems, there are some popular alternatives. Commonly used sliding motion assemblies are:
Slide-Mounted Systems
These roller systems are preferred because they can be operated at any angle without compromising safety. The system must be well balanced so it doesn't pull on the roller assembly causing damage or failure. A roller assembly mounted on a frame can be operated at angles of ninety-degrees or more. Since the system can be operated at angles greater than ninety degrees, it is not required that the roller assembly is completely vertical.
Linear-Rail Systems
This type of system is similar to the sliding system, but it requires an internal cam lever that secures the roller assembly to the rail and a shaft that engage the rollers. A roller system mounted on a rail assembly is less expensive than a sliding system, but the installation time is longer and more complex.
Roller Systems with A Fixed Drive Roller
These types of systems can be operated in either vertical or horizontal directions. They are easier to install and can accommodate much more torque.
Roller systems with a free-rotation mechanism are preferred over roller assemblies with a free-rotation mechanism. Since the roller is always operating in one position, a free-rotation mechanism is susceptible to interference and wear on the bearing housing and the bearing roller. This type of system can provide smooth motion but cannot perform as well as the two-piece rotating roller systems.
Комментарии